Friday, November 20, 2015
Thursday, November 19, 2015
Monday, November 16, 2015
Pump and signal combiner for bi-directional pumping of all-fiber lasers and amplifiers(10)
7. Signal feedthrough of the fiber combiner
Besides the pump power handling and the pump coupling efficiency of a fiber combiner, it is important for fiber laser and amplifier applications to maintain the optical properties of the signal light propagating through the fiber combiner. In particular, during the fabrication of the fiber component, externally induced mechanical stress and perhaps a marginal fraction of thermal diffusion of the core dopants [19] can result in a high signal insertion loss in conjunction with a degradation of the signal beam quality. This behavior was expected for large mode area DC fibers with a very low core refractive index (NA ~0.06), and therefore possible beam quality degradations of the signal feedthrough light was investigated (in Section 7.1).
The uninterrupted signal core in the fiber combiner provides the possibility of passing a signal beam through the combiner in forward and backward direction. However, in the case of a backward propagating signal, the pump diodes need sufficient protection against the signal. Thus, in Section 7.2 we investigate the signal to pump isolation of a 4 + 1x1 fiber combiner in a fiber amplifier setup.
7.1 Signal insertion loss and beam quality
In order to determine possible beam quality degradation and a signal insertion loss caused by the signal feedthrough of the combiner, the setup depicted in Fig. 14
Fig. 14 Setup for beam quality measurements, TF: target fiber, PBS: polarization beam splitter.was used. A signal at a wavelength of 1064 nm was launched into the core of a 2.75 m long Ytterbium-doped DC fiber (Nufern YDF-25/250), which is specified with a signal core diameter of 25 µm (NA 0.06) and a pump core diameter of 250 µm (NA 0.46). Thus, the parameters of the passive TF of the combiner were matched to the active fiber. The coiling diameter of the active fiber was 12 cm to maintain near diffraction limited beam quality [20]. The transmitted signal had a power of about 200 mW and was propagating in reverse direction through the fiber combiner. The beam quality measurements were carried out with a Fabry-Perot ring-cavity. With this cavity it was possible to determine the power fraction in higher-order transversal cavity modes with respect to the Gaussian TEM00 mode by scanning the length of the ring-cavity over a free spectral range (FSR). A detailed description of the measuring setup can be found in Ref [21]. Due to the use of a polarization sensitive beam quality measurement, a half- and a quarter-wave retardation plate in conjunction with a polarization beam splitter (PBS) were used. The determined polarization extinction ratio was better than 17 dB after the propagation of the signal through the active fiber and the fiber combiner.
Before the fusion splice between the active fiber and the 4 + 1x1 combiner, the power in higher-order modes of the active fiber was determined. This measurement served as a reference beam quality for the active fiber. The mode scan in Fig. 15(a)
Fig. 15 Normalized transmitted intensity through a premode cleaner as a function of the ring-cavity length in units of a free spectral range for (a) the reference beam and (b) the signal feedthrough beam of a 4 + 1x1 fiber combiner.
shows the logarithmic normalized intensity over a free spectral range for the reference beam with a power in higher-order modes of 3.1%. This results in a fundamental fiber mode power of at least 96.9% for the reference beam. For the signal feedthrough of the fiber combiner, a power in higher-order modes of only 5.1% was found (Fig. 15(b)).
Consequently, the signal feedthrough fiber (0.7 m long TF) only led to an increase in power in higher-order transversal modes of maximal 2%. Furthermore, it must be considered that additional power transfer to higher-order transversal modes can also be caused by the fusion splice between the active DC fiber and the TF. Hence, good preservation of the signal beam quality, in conjunction with the low signal insertion loss of less than 3%, provides an excellent high power fiber component for monolithic fiber laser and amplifier systems.
Thursday, October 29, 2015
Work Theory of the Laser Cutting Machine(2)
Cutting methods of laser cutting machine
Vaporization cutting
It means that vaporization is the main way to remove the processed material. In the process of vaporization cutting, workpiece surface is heated to vaporization temperature quickly by focused laser beams, forming High pressure steam and spraying outward at supersonic speeds. In the meantime, a hole is formed in the laser active area and laser beams reflex several times in the hole to increase the absorption of laser pump power combiner by material.
When high-pressure vapors spray outward, the melted materials are blown away in the kerf till the workpiece is finally cut. Vaporization cutting needs very high power density, which is eighth power of ten watt above per square centimeter. It is usually applied in low flash point materials and refractory materials.
Reaction Fusion Cutting
When assistant airflow not only blows the melted materials from the kerf but also has thermal reaction with the workpiece, this is the so-called reaction fusion cutting. Gases that can have reaction with workpiece are oxygen or mixture gases containing oxygen. When the surface temperature of workpiece reach to ignition temperature, strong combustion heat release occurs to improve the laser cutting ability.
Combustion heat release of low carbon steel and stainless steel is 60%. And it is about 90% for reactive metals like titanium.
Compared to vaporization cutting and general fusion cutting, reaction fusion cutting need less laser power density. However, reaction fusion cutting may effect the performance of worpiece since the combustion reaction can lead to chemical reaction on materials.
Fusion Cutting
When adding a assistant airflow system coaxial with laser to blow the melted materials away from kerf, this kind of cutting is fusion cutting. In fusion fiber coupler cutting, workpiece needn't to be heated to vaporization temperature so the required laser power density is reduced greatly.
Laser Scribing
It is mainly used in semiconductor materials, in which laser of high power density make a shallow groove in the semiconductor materials of the workpiece and then makes it crack through mechanistic or vibratory methods. The quality is valued by the surface fragments and size of heat affect area.
Cold Chipping
It is a new processing method, which is put forward along with ultraviolet band superpower excimer laser appeared in recent years. The basic theory is that energy of ultraviolet photons is similar to binding energy of many organic materials; this high-energy photons are used to impact bond organic materials thus make it crack, achieving purpose of cutting. This new technology has promising application future, especially in electron industry.
Thermal Stress Cutting
Mechanism of thermal stress cutting is that laser beams heat an area of fragile material to produce evident temperature gradient. The high surface temperature makes expansion and inner lower temperature hinders expansion, forming pulling stress in the surface and radial crushing stress inside. When the two stresses exceed fracture limit strength of the workpiece, crackle appears. And then the workpiece is broken along the normal direction of the crack. It is suitable for glasses and ceramics.
Conclusion: laser cutting machine is a cutting technology of melting and gasifying surface material through focused energy generated by the use of laser specialties and focused lens. It features good cutting quality, high speed, various cutting material and high efficiency.
About DK Photonics
DK Photonics – www.dkphotonics.com specializes in designing and manufacturing of high quality optical passive components mainly for fiber laser applications such as 1064nm high power isolator, Cladding Power Stripper, Multimode High Power Isolator, pump combiner,1064nm Band-pass Filter,(6+1)X1 Pump and Signal Combiner, PM Circulator, PM Isolator, optical Coupler. More information, please contact us.
Tuesday, October 27, 2015
Work Theory of the Laser Cutting Machine(1)
Laser has been applied in teaching, military as well as industrial production. Laser cutting machine is one of the applications. It can be used in both metal and non-metal cutting, Melting surface material by laser beam. This article will discuss the work theory of laser cutting machine.
Introduction on the work theory of laser cutting machine.
Laser cutting machine adopts the energy released on the time when laser beam irradiate metal surface. The metal is melt by laser and sinter is blow away by gas. Because laser power is highly focused, only a very little heat effects the other part of metal plate and causes a little or no deformation. Laser can cut any complex shape precisely, which needs no further processing.
Laser source is generally CO2 laser beam high power isolator with operating power of 500~5000W. The power is even lower than that of many household electric heater, and because of lenses and reflectors, laser beams are focused in a very small bit of area. Highly focused energy heat the area quickly and makes the metal plate melted.
Laser cutting machine can cut stainless steal of thickness less than 16mm; when adding oxygen in laser beam, the cutting thickness is 8~10mm but it will generate a thin oxidation film in the cut surface. The maximum thickness is 16mm which leads to larger cutting deviation on the size of components.
Since the advent of laser, numerous laser products have been developed, such as laser printer, laser cosmetic instrument, laser marker, laser cutting machine etc. Due to its late start in China, the laser technology in China is greatly behind the developed countries. Although Chinese manufacturers can produce plenty of laser products, some key parts such as laser tube, driving motor, galvanometer and focus lens are imported products. This leads to an increase on cost thus an increase on consumer's payment.
In recent years, domestic research and production of laser products become closer to advanced overseas products with the progress of laser technology in China. Some aspects are even superior to products abroad, which has a leading role in market because of the advantages of price. Overseas products have absolute predominance in precision machining for its quality on stability and endurance.
Work theory of laser cutting machine
Laser tube is the core part of laser cutting machine. So, below is an introduction of the most popular laser tube. CO2 laser tube.
Laser tube is composed of hard glasses, so it is fragile. It adopts layer of sleeve construction with discharge tube in the most inside layer. However, the diameter of discharge tube is thicker than laser tube, diffraction between the thickness of discharge tube and the size of flare is in direct ratio; the length of tube is in proportion to output power of discharge tube. Laser tube generates a large quantity of heat in the operation of laser cutting machine, which influences the normal work. So cold water machine is needed to cool laser tube, ensuring constant temperature for successful running.
Cutting features of laser cutting machine
Advantages of laser cutting:
One — high efficiency
Laser cutting machine is always connected to several numerically-controlled rotary tables to achieve numerical controlled cutting. It only needs to change the NC program to adjust to components of different shapes, which can make 2D cutting as well as 3D cutting.
Two — high speed
When cutting low carbon steel sheets of 2mm thickness, the speed of 1200W laser cutting is 600cmmin; when it is 5mm thick polypropylene resin plate, the cutting speed is 1200cmmin. The material needs no clamping fix in laser cutting process.
Three — high quality cutting
Laser cutting features thin kerf. The two sides of kerf are parallel and the kerf is vertical to the surface. The cutting precision can reach to ±0.05mm. The cutting surface is clean and nice, with roughness of tens of microns. The cut components can even come into use directly without further machining. After laser cutting, the heat effected area is very small and material near to kerf has not been affected, making little deformation, high cutting precicion and perfect geometrical shape
Four — non-contact cutting
Laser cutting is non-contact cutting, which means no tool wear problem. When processing different shapes, there is no need to change tools, the only way is to alter the output parameter of laser. The whole laser cutting process features low noise, little vibration and little pollution.
Five — various cutting material
Compared to oxyacetylene cutting and plasma cutting, laser cutting can be applied on more materials, including metal and non-metal, metal matrix and non-metallic matrix composite, leather, wood as well as fibers.
About DK Photonics
DK Photonics – www.dkphotonics.com specializes in designing and manufacturing of high quality optical passive components mainly for fiber laser applications such as 1064nm high power isolator, Cladding Power Stripper, Multimode High Power Isolator, pump signal combiner,1064nm Band-pass Filter,(6+1)X1 Pump and Signal Combiner, PM Circulator, PM Isolator, optical Coupler. More information, please contact us.
Wednesday, September 23, 2015
Pump and signal combiner for bi-directional pumping of all-fiber lasers and amplifiers(9)
6. Demonstration of 440 W pump power handling
After detailed theoretical and experimental characterization of fiber pump combiners with multiple pump ports, a pump power handling performance test was conducted. For these investigations each pump port of a 4 + 1x1 combiner was connected to a fiber coupled pump diode (nLight Pearl) with an output power of ~110 W at a wavelength of 976 nm. The PFF and the delivery fiber of the pump diode had a core diameter of 105 µm with a NA of 0.22. At each fiber output end of the IF, a pump light stripper was applied to avoid the Fresnel reflection of the TP, and therefore the TP was not measured. Up to the maximum total pump diode power of 440 W, a coupling efficiency of 90.2% was experimentally determined (Fig. 13
Fig. 13 Combined pump power for a 4+1x1 high power fiber combiner, * ratio of coupled power to total diode power in percent.
). In the simulations a slightly higher coupling efficiency of 92.8% was obtained. The difference of 2.6% in simulated and measured pump light coupling must be distributed among TP, PAA and PCT, with simulated values of 3.0, 1.4 and 1.7%, respectively. It can be assumed that the PAA-fraction is higher than 1.4%, since the fibers of the combiner are contaminated with dust particles in spite of intensive cleaning. If we assume for each individual loss mechanism an error of 1% related to the total diode power then PCT was 7.5 W ± 4.4 W, i.e. the coating of the TF and the pump power stripper had to handle this fraction of power.
About DK Photonics
DK Photonics – www.dkphotonics.com specializes in designing and manufacturing of high qualityoptical passive components mainly for fiber laser applications such as 1064nm high power isolator,Cladding Power Stripper, High Power Isolator,pump combiner,1064nm Band-pass Filter,(6+1)X1 Pump and Signal Combiner,PM Circulator,PM Isolator,optical Coupler.More information,please contact us.
Monday, September 14, 2015
Pump and signal combiner for bi-directional pumping of all-fiber lasers and amplifiers(8)
Pump and signal combiner for bi-directional pumping of all-fiber lasers and amplifiers(8)
5.2 Simulations of the loss mechanism caused by additional pump ports
As already discussed, the total power loss is comprised of TP, PAA and PCT. Since a TL of 20 mm and a TR of 6 seem to be promising parameters for a fiber combiner with multiple pump ports, Fig. 9
Fig. 9 Simulated losses for a pump combiner with a TL of 20 mm and a TR of 6 providing up to 6 pump ports. Please see Fig. 1for TP, PCT and PAA.
illustrates the behavior of the 3 different loss mechanisms and the total power loss against the number of pump ports. The input pump light NA of the PFFs was 0.22. The simulations clearly show that the TP-fraction as well as the PAA-fraction increase with the total power loss, and the PCT-fraction stays almost constant. The NA-mismatched pump light, which couples into the coating of the target fiber (PCT) can be kept below 1.7%, even up to 6 pump ports. Hence, an increasing number of pump ports and, therefore, scaling of the combined pump power results in additional power losses, but with an insignificant increase of thermal load to the coating of the TF. Of course, due to an increased PAA the combiner housing would be exposed to a higher thermal load, but this can be handled by an adequate thermalconcept. The increased PAA can be explained by pump light rays which couple back from the TF into one of the IFs, further propagate in the converging taper portion of the IF, increase in NA and undergo refraction into the ambient air. The increase of the TP-fraction with additional pump ports can be caused by pump light rays with a low NA which reverse couple into one of the IFs and further propagate there.
Finally, the simulations show that the total pump power loss increases with each additional pump port but the PCT, resulting in thermal load of the TF, does not increase significantly compared to a fiber combiner with a single pump port. In general, for the optical design of a side-pumped coupler with multiple pump ports, a TL as short as possible in conjunction with a TR as low as possible, but still satisfying the required pump coupling efficiency for the desired number of pump ports, ensures efficient pump light combining with low power losses. In contrast, for a single pump port, a longer TL in conjunction with a low TR is advantageous for increasing the pump coupling efficiency and reducing PCT-losses in particular.
5.3 Experimental characterization of pump combiners with multiple pump ports
Since the simulation results indicate that a TL of 20 mm and a TR of 6 are useful taper parameters, fiber combiners with two, four and six pump ports were developed. Each pump port consisted of an IF with a measured TL of 18 mm and a measured TR of 6.7. Each PFF had a NA of 0.15, and to characterize the combiner was connected to a pump diode (Oclaro BMU25) with a pigtail fiber delivering a maximum output power of about 25 W at a wavelength of 976 nm. The delivery fiber of the pump diode had parameters identical to the PFF.
Figure 10(a)
Fig. 10 (a) Combined and transmitted power measured for a fiber combiner with 4 pump ports and (b) combined pump power measured for a fiber combiner with 6 pump ports, * ratio of coupled or transmitted power to total diode power in percent.
shows the total diode power with respect to the combined pump power and TP for a fiber combiner with four pump ports. For the combined pump power a coupling efficiency of 92% (93.1% in the simulation) was measured, and the fraction of TP was 3.6% (3.9% in the simulation) compared to the total diode power. Thus, the measured TP of 3.6% was 45% of the total power loss of 8% (Fig. 10(a)). Based on the good agreement between simulation and experiments it can be assumed that the PCT-fraction and PAA-fraction were about 0.6% and 2.3% of the total diode power, respectively.
Microscope images of the top view and of the cross section view, close to the taper waist, of a fiber combiner with 4 pump ports are depicted in Fig. 11(a)
Fig. 11 Microscope image of (a) the top view and (b) the cross section view of a fiber combiner with 4 pump ports.
and 11(b).
The experimental results of a developed six pump port fiber combiner with a combined pump power of 141.5 W and an obtained coupling efficiency of 89.6% (91.1% in the simulations) is shown in Fig. 10(b). The fiber combiner with six pump ports was limited by the available pump power and not by thermal problems. For the combiner presented in Fig. 10(b), Fig. 12(a)
Fig. 12 (a) Pump coupling efficiency of the individual pump ports of the six pump port fiber combiner presented in Fig. 10(b) and10(b) comparison of the experimentally achieved pump coupling efficiencies with the simulation results for fiber combiners with multiple pump ports.
shows the pump coupling efficiency of each individual pump port with a maximum and minimum pump coupling efficiency of 90.2 and 88.8%. The difference of only 1.4% indicates a very homogeneous fiber bundle structure, and supports the assumption of identical optical behavior of the individual pump ports.
An overview of the experimentally obtained coupling efficiencies with the corresponding simulation results for a fiber combiner with 1, 2, 4 and 6 pump ports is depicted in Fig. 12(b). An agreement of the experimental and simulated results within 1% confirms the applicability of the simulation approach for multiple pump ports. For each fiber combiner a TL of 18 mm, a TR of 6.7 and a PFF with a core NA of 0.15 was applied.
About DK Photonics
DK Photonics – www.dkphotonics.com specializes in designing and manufacturing of high qualityoptical passive components mainly for fiber laser applications such as 1064nm high power isolator,Cladding Power Stripper,Multimode High Power Isolator,pump combiner,1064nm Band-pass Filter,(6+1)X1 Pump and Signal Combiner,PM Circulator,PM Isolator,optical Coupler.More information,please contact us.
Wednesday, September 2, 2015
Fiber Laser Welding: Some Traits and Applications(2)
Technological parameter of laser welding:
(1) Power density
Power density is one of the key parameters in laser processing. When the power density is relatively high, the surface would be heated to boiling point in microseconds, thus generate mass vaporization. As a result, high power density is good for material removal processing such as punching, cutting and carving. When the power density is relatively low, it would take some microseconds to meet the boiling point, the bottom can reach the melting point before vaporization occurs, thus a good melt welding is successfully formed. So the power density ranges from 104~106W/cm2 in conductive laser welding.
(2) Laser pulse shape
Laser pulse shape is an important question in laser welding, especially for foil welding. When high strength laser beam reaches the material surface, 60~98% of the laser energy will be lost by reflection and the reflectivity is changeable by the temperature of the material surface. The reflectivity of metal can vary greatly in a laser pulse period.
(3) Laser pulse width
Laser pulse width is an important parameter to distinguish material removal and material melting; it is also a key parameter to decide the cost and volume of processing equipment.
(4) Influence of defocusing amount on weld quality
There are two ways of defocus: positive defocus and negative defocus. It is positive defocus when focal plane is above the workpieces, vise versa. According to geometry optical theory, when positive and negative defocusing plane equals to welding plane, the power densities are almost the same in the corresponding panels, but the actual laser pools have different forms. It can achieve larger depth of fusion when it is negative defocus.
Application field of laser welding
Laser welding machine has wide application in manufacturing industry, powder metallurgy field, automobile industry, electronics and some other fields.
Source : demarlaser
Application of laser welding in automobile industry
Volkswagen AG has adopted laser welding in car roof of brands like AudiA6, GolfA4 and Passat. BMW and GM have used laser welding in top of the car frame while Mercedes-Benz has applied laser welding in drive disk assembly. Except for laser welding, other laser technologies have be applied as well. Companies like Volkswagen GM, Benz and Nissan have used laser to cut covering parts while FIAT and Toyota have adopted laser for coating engine exhaust valve; Volkswagen has used laser for surface hardening on engine camshaft. Domestic vehicle models like Passat, Polo, Touran, Audi, Dongfeng Peugeot and Focus have adopted laser welding technology.
Independent automobile brands like Brilliance, Chery and Geely have adopted laser welding as well.
Improvement and development of new laser welding technology
Laser welding technology is continuously developing along with the progress of the time. The following three technologies can help expanding laser's application scop and enhancing the automatic control level of laser welding.
- filler wire laser welding
Laser welding generally doesn't fill wires but has high requirement on assembling clearance, which is hard to be guaranteed thus limits the application scope. Filler wire laser welding method has lower requirement on assembling clearance. For example, if the aluminum alloy plate is of 2 mm's thickness, the clearance must be zero for a good shaping. When adopting φ1.6mm welding wire as filler metal, it can form good shape even the clearance is 1.0 mm. Besides, filler wire can be used for adjusting chemical components and multi-layer welding on thick board.
- Beam rotation laser welding
By the adoption of laser beam rotation laser welding methods, demands on welding assembly and beam centering are reduced greatly.
- On-line detection and control of laser welding quality
It is becoming a hot researching topic on detecting laser welding process by using plasma such as light, sound and electric charge; some researches have achieved closed-loop control.
DK Photonics – www.dkphotonics.com specializes in designing and manufacturing of high quality optical passive components mainly for fiber laser applications such as 1064nm high power isolator, Cladding Power Stripper, Multimode High Power Isolator, pump combiner,1064nm Band-pass Filter,(6+1)X1 Pump and Signal Combiner, PM Circulator, PM Isolator, optical Coupler. More information, please contact us.
Monday, August 31, 2015
Fiber Laser Welding: Some Traits and Applications(1)
What is fiber laser? The world's first laser beam is produced in 1960 by the use of flashbulb stimulating ruby crystalline grain. Limited by the thermal capacity of the grain, the pulsed beams is short and the frequency is very low. Although the instantaneous pulse peak can reach up to 106W, it still belongs to low energy output.
Source:tamu.edu
Laser technology adopts the beams of light generated by the reflection of laser from polariscope and congregates the beams in focusing device to generate beams with enormous energy. Once the focus is approaching, the workpieces will be melt or vapored in some milliseconds. This opens up a new welding application domain for high power CO2 and high power YAG laser. The key of laser welding equipment is high power laser, including solid laser and gas laser. Solid laser is the so called Nd:YAG laser. Nd is a rare earth elements and YAG represents Yttrium Aluminum Garnet, with similar crystal structure as ruby. The wavelength of Nd:YAG laser is 1.06μm. It can produce beam transmitted by fiber, so it can simplify beam delivery system, which is suitable in flexible manufacturing systems and remote working as well as high welding precision workpieces. Nd:YAG laser of 3-4 KW output is commonly used in automobile industry. Gas laser is the so-called CO2 laser. Its working medium is molecule gases which can generate iraser of 10.6μm in average. It can work continuously and output very high power; the standard laser power is between 2-5 KW.
The major traits of laser welding are as following:
- The welding is fast and deep with little deformation.
- It can work in room temperature and disparity conditions with simple equipment and device. For example, the laser beam will not offset; laser welding can be really carried out in vacuum, air or any gas environment, or even through glass or any transparent material.
- It can weld refractory materials as titanium and quartz and anisotropic materials with good effects.
- When welding, depth-to-width ratio can reach to 5:1 and the highest can reach up to 10:1.
- It can applied in microwelding. Slight flare can be generated by focused laser beams which can positioning precisely and be applied in mass automatic production of micro and small workpieces' installation and welding.
- It is flexible in welding areas that is difficult to access. Especially in recent years, the adoption of optical fiber transmission in YAG laser processing technology has greatly promoted the popularization and application of laser welding technology.
- Beam split is easy to be realized by time and space and multiple beam can be processed all at once, providing conditions for more precise welding.
However, there are some limits of laser welding:
- It requires high assembly accuracy for weld and it should has no obvious deviation of beam on workpieces. It is because that the flare is too small and the welding line is too narrow. If the assembly accuracy and beam position cannot meet the requirements, it is easy to make weld defect.
- The cost and initial investment on laser and the relevant systems are high.
Resource : avio
DK Photonics – www.dkphotonics.com specializes in designing and manufacturing of high quality optical passive components mainly for fiber laser applications such as 1064nm high power isolator, Cladding Power Stripper, Multimode High Power Isolator, pump combiner,1064nm Band-pass Filter,(6+1)X1 Pump and Signal Combiner, PM Circulator, PM Isolator, optical Coupler. More information, please contact us.
Friday, August 28, 2015
The Comparative Between Fiber Laser Cutting Machine and CO2 Cutting Machine
Cutting is one of the most widely applied laser processing techniques. Fiber laser and CO2 laser are the most commonly used laser cutting equipment. It is necessary for users to have a knowledge of the advantages and disadvantages of both the two ways of cutting.
Source : fe.infn
Wavelength of fiber laser is 1.06μm and Wavelength of CO2 laser is 10.6μm. Both are infrared light and can be absorbed by material so that they can be applied in Industrial material processing. Fiber laser is unable to be applied in non-metal cutting, such as wood, plastic, leather and ramie cotton fabric. In case of non-metal cutting, CO2 laser is the only choice. But CO2 laser cannot cut copper products, including brass and red copper. Because copper is highly reflective material for CO2 laser, laser will be reflected instead of absorbed by copper, which can cause harm.
Laser is evaluated by integrated index as cutting speed, drilling efficiency and section quality.
Fiber laser has an advantage in cutting thin plate, especially for thickness under 3mm. Its maximum cutting speed ratio can reach to 4:1 and 6mm is critical thickness for the two kinds of lasers. When it is thicker than 6mm, fiber laser shows no preferential; as the thickness increases, CO2 laser shows preferential gradually but not outstandingly. Generally speaking, fiber laser has an advantage in cutting speed.
Drilling efficiency:
Before cutting, laser beam should penetrate workpiece. Fiber laser needs more time in drilling than CO2 laser. Take 3KW optical fiber laser and CO2 laser as an example, The latter saves 1 second in drilling 8mm carbon steel; and 2 seconds in 10mm drilling. As thickness grows, CO2 laser will save more time.
Source : nufern
Section quality:
Section quality usually means the roughness (surface perfection) and perpendicularity.
When cutting steel plate under 3mm, section quality of fiber laser is worse then CO2. As thickness grows, the difference becomes more obvious.
In addition, carbon steel plate has high absorptivity on fiber laser energy, so it has shortcoming in cutting holes (aperture < panel thickness).
The above comparison will help users make a reasonable choice. The cutting speed of the two lasers is equally matched. Fiber laser is inferior to Co2 laser in section quality and drilling efficiency. There is no quick answer to which is better. They both have advantages and disadvantages in specific application demands.
By the way, laser cutting precision has nothing to do with the adoption of lasers. It is determined by machine positioning precision, resetting precision and consistency of kerf width. Fiber laser has narrower kerf than CO2. Kerf width doesn't affect precision of the parts either, since it can be offset by cutting gap compensation.
DK Photonics – www.dkphotonics.com specializes in designing and manufacturing of high quality optical passive components mainly for fiber laser applications such as 1064nm high power isolator, Cladding Power Stripper, Multimode High Power Isolator, pump combiner,1064nm Band-pass Filter,(6+1)X1 Pump and Signal Combiner, PM Circulator, PM Isolator, optical Coupler. More information, please contact us.
Thursday, July 30, 2015
Field-Terminated Fusion Splice-On Connector-North American Market Forecast
According to ElectroniCast, the quantity of field-terminated fiber optic splice-on connectors in North America will increase at an explosive annual rate of 41.9% …
ElectroniCast Consultants, a leading market research & technology forecast consultancy addressing the fiber optics communications industry, today announced the release of a new market forecast of the consumption of field terminated fiber optic fusion splice-on connectors in North America.
Field terminated fiber optic fusion Splice On Connectors (SOC) are installed for rapid repairs or for limited space situations where pre-terminated fiber cabling may be difficult, such as when the cable assembly needs to pass through small openings such as conduit. The splice-on connectors are an option when the precise length of the optical fiber link is not pre-determined and a field-installed termination solution is required, such as in Fiber to the Home (FTTH) and other communication applications.
Last year, 306-thousand field-terminated fiber optic fusion splice-on connectors were installed in non-OEM applications in North America. The number of connectors is forecast to increase at an explosive rate of 41.9% per year, reaching 2.49 million units in 2020. Market forecast data in this study report refers to consumption (use) for a particular calendar year; therefore, this data is not cumulative data.
The Telecommunications application category is forecast to maintain the leadership in relative market share through the year 2018, until the Premises Networks application category is set to capture the lead. Telecommunication use is forecast for 35.5% annual growth in quantity (2014-2020), mainly driven by access optical fiber deployment. The Cable TV application is also driven by the use of connectors for FTTH (Home) and FTTB (Building/MDUs – Multiple Dwelling Units).
The market forecast segments the connectors by single-mode and multimode optical fiber, as well as into the following types: MPO, LC, FC, ST, SC, and other. The use of single mode fiber optic field-terminated fusion splice-on connectors in North America is forecast to increase from 173.8-thousand units in 2014 to 1.49 million in 2020. Multimode fiber is best suited for use in short lengths, such as those used in datacom and specialty networks and in 2020, multimode connectors are expected to reach 1-million units.
“In 2014 in North America, 4.3-thousand new fusion splicers were brought into Premises Datacom, and the use of field terminated fusion splice on connectors is a major market driver for the use of fiber optic fusion splicers used in premises network applications, the data center (DC) and longer link length datacom cable installations,” said Stephen Montgomery, Director of the ElectroniCast market study.
“The SOCs are emerging as a viable alternative to pre-terminated fiber optic cables (pigtail and cable assemblies/ patch cords). Also, based on primary research interviews with network planners and installers, we are finding that field terminated fusion splice-on connectors are rapidly being accepted as a go-to solution. With SOCs, communication network technicians can install reliable cable links with exact lengths, eliminating cable shortness or excess slack that is typically a result with the pre-terminated cable solution,” Montgomery added.
Tags: CWDM Multiplexer, DWDM Multiplexer,19" rack mount chassis CWDM, ABS plastic box, CWDM MUX/DEMUX Module, LGX CWDM Module,8CH CWDM Module, 16CH CWDM Module
Wednesday, July 15, 2015
The Modern Data Center – Modular Data Center
The modern data center is a complex place. The proliferation of mobile devices, like tablets and smartphones, place an ever-increasing pressure on the IT departments and data centers. End-user and customers’ expectation levels have never been higher and the demand for data shows no sign of slowing down. Data center managers must manage all of these elements while also remaining efficient and keeping costs under control. So where does the data center go from here?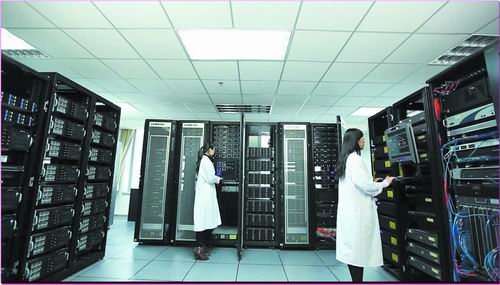
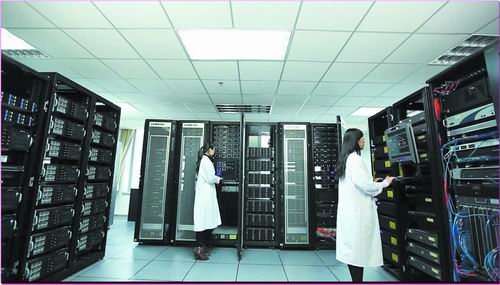
One thing I have noticed in the evolution of the modern data center is that the facilities are gaining importance; improving energy efficiency and IT management have come to the forefront. Maximizing the organization’s resources is vital, and that means delivering more to facilities and equipment without expending more on staffing. IDC forecasts that during the next two years, 25 percent of all large and mid-sized businesses will address the power and cooling facility mismatches in their data centers with new IT systems and put a 75 percent cap on data center space used. So there again is the crucial challenge of doing more and innovating while keeping budgets and spend under control.
Another key part of the next generation data center mix is automation. Today’s data center manager is engaged in sourcing the right automation tools that will help them manage energy consumption and add new technology without disrupting normal operations. These are a few of the key challenges in the modern data center—so data center managers and IT departments must find ways to address them.
Where does the Data Center Go Next?
At the heart of data center evolution is the information technology sector’s rapid rate of change. Many new products and services must be implemented with much less time to value, and data centers need to be agile enough to assess and accommodate them all. If you examine enterprise data centers, then you might observe the ways that cloud computing and hyperscale innovations are displacing traditional enterprise systems, with new paradigms pioneered by innovators like Amazon and Google. With new options being developed, enterprises now have to chart strategies for cloud computing, including public, private or hybrid cloud. Gauging where the technology will go next is difficult to tell. Will the traditional vendors, such as Cisco and EMC, prevail or will new paradigms from Nutanix or Simplivity disrupt and displace these traditional data center dominators?
The race is on to manage the rapid rate of change while also staying agile, meeting end-user expectations and managing costs. For example, data center managers must handle the level of capacity their data center requires while ensuring they don’t overspend on unused capacity. This is where the focus on data center design comes into play.
Taking the Data Center Forward
These specific needs and challenges that the modern data center faces require working with the right tools and solutions. Modular, purpose-built data center infrastructure allows organizations to develop data center services based on need—when capacity rises and where capacity is needed. For example, we’ve observed in Singapore that most data centers operate slightly above 2.1 Power Usage Effectiveness (PUE). This means that companies spend more on cooling their data center rather than on operating and powering the IT equipment. It is a simple challenge—drive efficiency without impacting operations. You want to drive PUE down to approximately 1.06, regardless of where you need to operate, and reap huge energy savings while better serving customers. If done right, there is a positive environmental impact.
Changing the paradigm of the traditional data center enables organizations to reap these rewards. Assessing and establishing business objectives that reflect what is possible, rather than what always has been or what is easier and more comfortable, has led to innovative services and new business models that reset the competitive standards for everyone. Better PUE is a mandatory step in this process. The PUE journey continues as evidenced by Amazon, which had recently taken to harnessing wind to power its data centers. Modular data centers will play a major part in this PUE journey, thanks to more efficient use of energy and greater flexible support for resiliency and compute density.
Wednesday, June 3, 2015
How much do you know about CWDM Multiplexer and DWDM Multiplexer
CWDM multiplexer and DWDM multiplexer are two main products of WDM multiplexer. The full name of WDM, CWDM and DWDM are wavelength division multiplexing, coarse wavelength division multiplexing and dense wavelength multiplexing respectively. How much do you know about them? If you have no idea, the following introduction will help you a lot.
In the very first place, let's get to know what the WDM is. Based on a single fiber optic transmission, many optical signals that are loaded with information and have different wavelengths can be synthesized into one single beam by WDM multiplexer. Then, a special communication technology will be adopted to separate those optical signals at the receiving terminal. On the basis of WDM technique, the CWDM device and DWDM device are two popular products in the current market.
CWDM device
When it comes to the CWDM multiplexer, first of all, it provides service for metropolitan area network access layer, whose working principle is in line with WDM multiplexer. However, it simplifies the structure largely. For example, the filter film layer number of CWDM is just 50, while the WDM is as many as 200 layers. That is to say, the rate of finished products has been improved and the cost has been reduced largely. Besides low cost, the CWDM device is also advantageous in small volume, small power consumption, convenient maintenance and large transmission capacity. The laser device in the system doesn't need semiconductor refrigerator and temperature controller, which can lessen the power consumption obviously. However, the CWDM also has shortcomings. For instance, developing and simplifying the optical transceiver module and optical component is urgent to be solved.
DWDM device
As to the DWDM multiplexer, comparatively speaking, it makes the best use of fiber-optical bandwidth and enhances the message capacity of cellular system, which is well-known for simple dilatation and stable performance. Integrated system and open system are two dominant application systems of DWDM multiplexer, which are based on different wavelength conversion technologies. No matter which system is adopted, the free-running 1510nm wavelength will be chosen to carry OSC or optical supervisory channel so as to transmit information. Such an OSC is a comparatively independent subsystem, which offers maintenance and management information.
The last question is what advantages WDM technique has when compared with traditional transmission methods. Generally speaking, it includes such aspects as making best use of low-loss wave band, transmitting several optical signals in one optical fiber, good flexibility, low investment cost, excellent system reliability and fast and convenient recovery.
Tags: CWDM Multiplexer, DWDM Multiplexer,19" rack mount chassis CWDM, ABS plastic box, CWDM MUX/DEMUX Module, LGX CWDM Module,8CH CWDM Module, 16CH CWDM Module
Monday, May 25, 2015
Do you know these about CWDM Multiplexer and DWDM Multiplexer?
Do you know these about CWDM Multiplexer and DWDM Multiplexer?
Wavelength division multiplexing (WDM) is a technology or technique modulating numerous data streams, i.e. optical carrier signals of varying wavelengths (colors) of laser light, onto a single optical fiber. The goal of WDM is to have a signal not to interfere with each other. It is usually used to make data transmission more efficiently. It has also been proven more cost effective in many applications, such as WDM network applications, broadband network application and fiber to the home (FTTH) applications and so on. According to channel spacing between neighbored wavelengths, there are two main types of WDM, including Coarse WDM (CWDM) and Dense WDM (DWDM). Though both of them belong to WDM technology, they are quite different. Then, what are the differences between them? This paper will give you the answer.
Definition of CWDM
CWDM is a method of combining multiple signals on laser beams at various wavelengths for transmission along fiber optic cables, such that the number of channels is fewer than in DWDM but more than in standard WDM. “Course” means the channel spacing is 20nm with a working channel passband of +/-6.5nm from the wavelengths center. From 1270nm to 1610nm, there are 18 individual wavelengths separated by 20nm spacing.
Definition of DWDM
DWDM is a technology that puts data from different sources together on an optical fiber, with each signal carried at the same time on its own separate light wavelength. “Dense” refers to the very narrow channel spacing measured in Gigahertz (GHz) as opposed to nanometer (nm). DWDM typically uses channel spacing of 100GHz with a working channel passband of +/-12.5GHz from the wavelengths center. It uses 200GHz spacing essentially skipping every other channel in the DWDM grid. And it has also gone one step further using an Optical Interleaver to get down to 50GHz spacing doubling the channels’ capacity from 100GHz spacing.
CWDM vs DWDM
According to the content above, you will find some small differences between them. 16CH CWDM Module is defined by wavelengths and has wide range channel spacing. DWDM is defined by frequencies and has narrow channel spacing. What’s more, what other differences do they have?
Capacity of Data
In fiber optic network system, DWDM system could fit more than 40 different data streams in the same amount of fiber used for two data streams in a CWDM system. In some cases, CWDM system can perform many of the same tasks compared to DWDM. Despite the lower transmission of data through a CWDM system, these are still viable options for fiber optic data transmission.
Cost of Cable
CWDM system carries less data, but the cabling used to run them is less expensive and less complex. A DWDM system has much denser cabling and can carry a significantly larger amount of data, but it can be cost prohibitive, especially where there is necessary to have a large amount of cabling in an application.
Long-haul or Short-haul Transmission
DWDM system is used for a longer haul transmission through keeping the wavelengths tightly packed. It can transmit more data over a significantly larger run of cable with less interference. However, CWDM system cannot travel long distances because the wavelengths are not amplified, and therefore CWDM is limited in its functionality over longer distances. If we neeed to transmit the data over a very long range, DWDM system solution may be the best choice in terms of functionality of the data transmission as well as the lessened interference over the longer distances that the wavelengths must travel. As far as cost is concerned, when required to provide signal amplification about 100 miles (160km), CWDM system is the best solution for short runs.
According to the content above, maybe you have already understood some differences between CWDM and DWDM by the comparision of them from definition, capacity, cable cost and transmission distance etc. And here is also a figure of comparisons between CWDM and DWDM which may help you to consolidate your understanding of this paper.
Tags: 19" rack mount chassis CWDM, ABS plastic box, CWDM MUX/DEMUX Module, LGX CWDM Module,8CH CWDM Module, 16CH CWDM Module
Subscribe to:
Posts (Atom)